Condensing Heat Exchange
Greater energy savings by capturing both sensible and latent exhaust heat.
All exhaust heat exchangers operate in the exhaust stream of a boiler or other industrial combustion process. The waste heat gases from fuel combustion are channeled through the exchanger. A heat sink (liquid to absorb heat) flows through spiral finned tubes that line the inside of the heat exchanger. Exhaust heat is conducted through the fin tube raising the heat sink temperature while lowering the overall exhaust gas temperature.
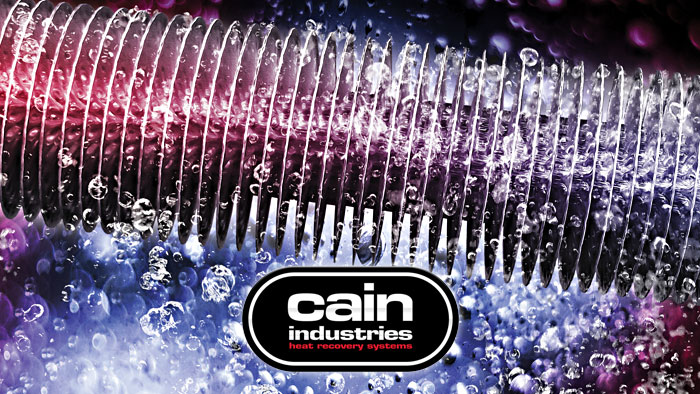
A more effective means of exhaust heat transfer is a condensing heat exchanger. It utilizes a colder heat sink with a greater entering temperature difference than exhaust stream gases. A heat sink of lower temperature absorbs sensible heat change in temperature, better than one of higher temperature. More importantly, the colder heat sink forces a "chemical reaction" of condensation within the exchanger. Microscopic water droplets start to form as the exhaust flows around the finned tube, cooling the gases to its dew point or below. Droplets grow in size on the tubing to form streams of running water. Vapor contained in the exhaust gases condenses into water transferring its latent energy to the heat sink. This gas to liquid transformation releases roughly 1,000 BTUs of heat for every pound of water created. Capturing both sensible heat and latent heat drastically increases overall exhaust heat recovery efficiency.
Cain Industries has dedicated years of research and development to create condensing heat exchange equipment that performs consistently in the most brutal of exhaust heat environments. Designed, engineered and hand-built in the USA to operate reliably for decades, this cost saving heat recovery method significantly reduces the fuel required to maintain boiler output as waste heat is transferred back into feedwater or makeup water... Saving energy and eliminating related pollution!
A two-stage condensing heat exchanger allows heat transfer for two independent heat sinks. Each of the combined exchangers can be engineered for different heat exchange yields.
We manufacture condensing heat exchange equipment for steam boilers, hot water boilers and most natural gas combustion applications where a cold water heat sink is prevalent. All condensation is safely captured and drained away from the exchanger, protecting the boiler or other combustion source. Heat sinks consist of boiler feedwater, makeup water, hot water return, hot water storage tank, condensate tank, swimming pool and other types of process water.
Contact Cain Industries today for the best in sensible and latent exhaust heat exchange! We'll calculate the exact performance of installed equipment with minimal end user input.
>We guarantee the performance of every condensing heat exchange unit we build!