Agriculture Exhaust Heat Recovery Case Study
Diavik Diamond Mine
Yellowknife, Northwest TerritoriesCanada Heat Exchange Focus:
HRSR - Heat Recovery Silencer Radial Series (11 units)
Installation consists of eleven HRSR-472D24.7SSP heat transfer models. Each unit is recovering 6,799,000 BTUs per hour from its paired Caterpillar 3612 engine. The heat sink temperature of 60% ethylene glycol mixture (695 GPM) is being raised from 202°F to 221°F by reducing the engine exhaust gas temperature from 811°F to 400°F (10,742 SCFM).
Payback vs. Fuel Savings (per unit)
Unit Cost: $163,150
Payback: 2.1 Months
Annual ROI: 563%
Annual Fuel Savings: $917,860
Life Expectancy Fuel Savings: $18,357,200 (20 years)
Summary:
Diavik Diamond Mines began production in 2003, with an annual diamond production of approximately ten million carats. Equipment and materials are transported on an ice road constructed annually, and open only from early February to early April. Diesel fuel is the largest commodity brought to the Diavik site.
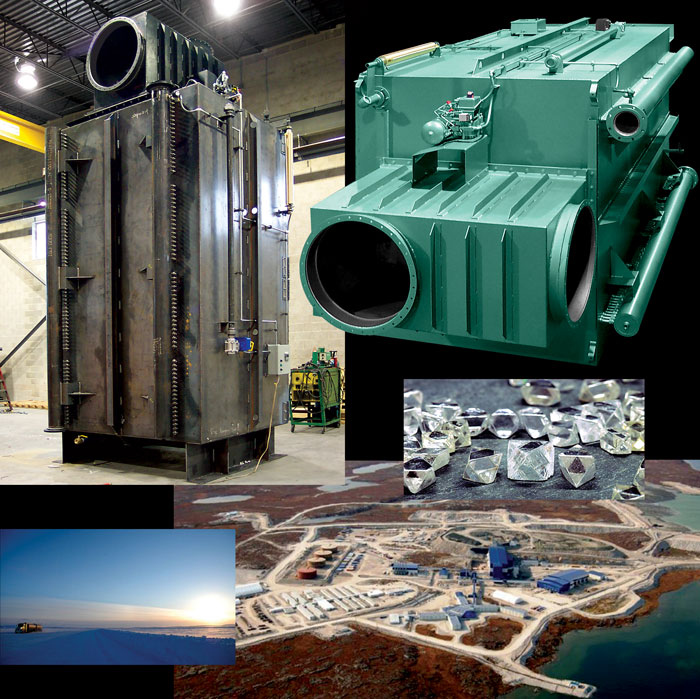