Ethanol Plant Exhaust Heat Recovery Case Study
Utica Ethanol Plant
Utica, WIUSA Heat Exchange Focus:
RTR - Rectangular Tube Recovery Series
Installation consists of one Cain RTR-166K25.7ALS heat transfer model. The unit is recovering 1,475,000 BTUs per hour from its paired 2,200 HP steam boiler. The heat sink temperature of the boiler feedwater (152 GPM) is being raised from 227°F to 247°F by reducing the boiler exhaust gas temperature from 367°F to 299°F (18,473 SCFM).
Payback vs. Fuel Savings (per unit)
Unit Cost: $37,902
Payback: 7.1 Months
Annual ROI: 168%
Annual Fuel Savings: $63,662
Life Expectancy Fuel Savings: $1,273,240 (20 years)
Summary:
Beginning production in 2003, Utica Energy, LLC became the 73rd ethanol plant operating in the USA. The plant has the capacity to store 3.5 million bushels of corn. In one day, Utica uses 42,000 kw/hr of electricity and 14,000 therms of natural gas. Utica is currently producing 52 million gallons of ethanol per year.
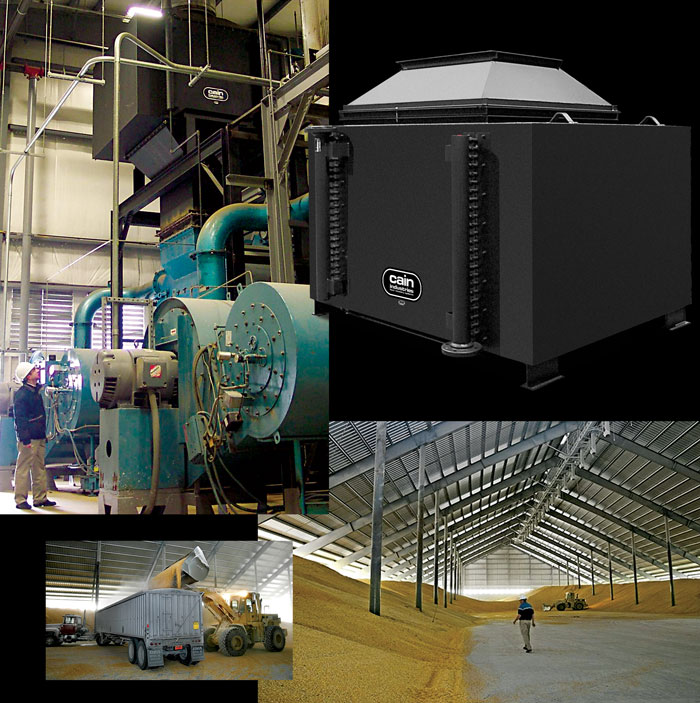